www.indo-industry.com
11
'11
Written on Modified on
To ensure the highest precision machining on its newest and largest portal milling machine, DMG chose REDEX drives: zero‐backlash rack & pinion drives and spindle drives
The DMG‐Portal Type DMU 600P milling machines have been designed to machine large components ‐up to 40 tons‐ at very high speed, dynamics and precision. Innovative drive systems are key contributing elements to this five axis system offering high versatility though a single setup. DMG works together with REDEX here. The European specialist in precision drives equips the X-, Y-, and C-axis with a TwinDrive rack and pinion drive system. REDEX precision drives are however also used in other drives axes and in the main milling spindle drive.
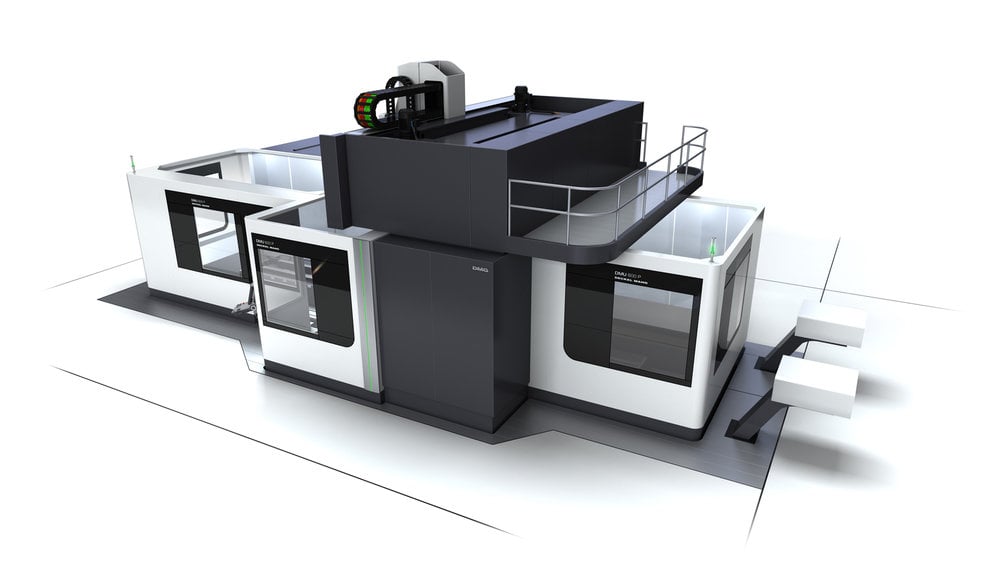
Maximum precision is required when manufacturing large precision tools such as large as molds or stamping forms for car body parts. Machining requirements for marine diesel engine housings are similarly high.
The tool part weighs several tons and are usually several meters long but every micrometer is crucial.
Precise machining of heavy components
DMG have developed the DMU P‐series portal milling machines for this exact purpose. The largest model in the series DMU 600P (Fig 1) is especially designed for precise, quick machining in XXL dimensions and performs milling and turning operations with high precision at maximum travels of 6000 x 4200 x 1500 mm (X/Y/Z‐Axis) and up to 2000 mm in the W‐axis. The rough parts weight may be up to 40 tons. At the same time the DMU 600P guarantees top speed and maximum flexibility since this machine has been designed for 5‐axis turning and milling in a single setup.
High precision with long travel lengths
One of the biggest challenges for the DMG designers was to guarantee such high level of machining precision at such large travel lengths (Fig. 2).
Linear drives play a central role here. Florian Garbarsky, Project Manager at DMG in Pfronten:
„The drives must have zero‐backlash with repeatable precision over thousands of operating hours and facing high forces directly related to the 60 kW power of the motor spindle.“
In figures: over a travel of 6 metres, an accuracy of up to +/‐ 0,0075mm is reached, with accelerations up to 3 m/s2. Thus, the highest level of accuracy, stiffness and the most constant temperature are considered as prerequisites when designing the complete machine. With these travel lengths and accuracy levels requests in hand, ball screws technology wasn’t considered to become a real challenger.
Rack & pinion drives
To guarantee the stiffness level, DMG designers have taken great care in selecting suitable drive systems. As said Florian Garbarsky: ‘’We carried out extensive benchmarking before to decide to use zero‐backlash rack & pinion drives from REDEX’’. Even in the C‐axis (the rotary axis of the spindle head), a ‘TwinDrive’ precision drive ensures high precision motion and positioning. It’s also noticeable that the two vertical ball screws of the W‐portal axis are synchronized through two SRP2 servo‐planetary reducers from REDEX.
Spindle Drive
In order to offer the high productivity high‐torque‐at‐low‐speed feature, a water cooled twospeed gearbox from the REDEX’ RAM series has been also mounted „inline“ (between the drive motor and the spindle inside the RAM).
X‐ and Y‐Axis: zero‐backlash „Twin Drive“‐ rack & pinion drive
According to its mechanical principle, there is always a certain backlash which affects the position accuracy on conventional rack & pinion drives. But this limitation does not apply to the TwinDrive‐Systems from REDEX, as the company has found a way to offer 100% zero‐backlash rack & pinion drives. The basic principle: two electronically synchronised complete drives are used in parallel, (motor + planetary reducer). One of the two servo motors serves as a drive, the other acts as a brake and thus ensures constant preload between the two pinions and the rack. This solution fully cancels the backlash and offers the most precise motion and positioning. And it’s this principle which was applied to the 6000 mm long X‐axis of the DMU 600P, as well as to the 4200 mm long Y‐axis and the C‐circular axis.
In the X‐axis, the turnkey drive solution DRP was chosen, including its two planetary drives with their two servo motors (Fig. 3).
In the Y‐axis the choice was rather to use the KRPX planetary reducers, which are fitted left and right on the Z‐carriage of the machine. And then, a DRP was used again on the spindle rotary axis (C‐axis). The machine’s CN electronic control then takes over the synchronisation and the preload for each of these TwinDrive systems.
High acceleration and maximum precision thanks to rigid linear drives
If the zero‐backlash feature of the drives is absolutely mandatory, it’s not enough by itself for reaching the requested level of maximum precision and best surfaces quality.
Just as important are the global stiffness, the control of temperature variations and an excellent transmission error accuracy – exactly the features which are the core strengths of REDEX planetary gearboxes. Thus the drives are extremely rigid in all directions, leading to outstanding positional accuracy, machined surface and repeatability.
To guarantee these features, the gearboxes are fitted with solid output bearings and the pinion is directly integrated into the pinion shaft. The bearing assembly itself consists of two pre‐loaded, oversized tapered roller bearings, which are fitted at the closest to the contact point of the pinions. The gearbox housing itself is machined extremely precisely and its design was widely optimized for offering maximum rigidity, whatever are the load directions.
This design not only guarantees very high torque rigidity, but also the best stiffness figures in all other directions, including the radial bending, which is ‐according to the extensive tests conducted by REDEX‐ responsible for almost 60 % of the total distortion in a rack & pinion drive application.
Thus, the bending is sharply reduced, and the axis natural frequency is highly improved allowing higher acceleration rates, heavier moved masses, while meeting higher precision requirements.
Benefits are not only technical, but also economical
Last but not least, for DMG, REDEX’s drive concept wins the argument not only from a technical viewpoint but also from an economic perspective.
According to an extended cost study by the OEM, optimum TCO* offered by REDEX for a travel of
6 m on the X‐axis with its rack & pinion drives cannot be beaten by any other technical solution of similar accuracy.
A multi‐facetted concept
The extended REDEX’ products range dedicated to Machine‐tool Drives applications allows engineers to make their choice in an almost unlimited library of drives, whatever are their level of technical requirements.
REDEX offer its Rack & Pinion concept in different variants – for instance with mechanical or electrical pre‐load, whereby DMG opted for electrical synchronization. On the other hand the systems may include any of the usual types of servo motor and gearbox/ gearbox assemblies.
For the DMU 600P C‐axis, (the spindle’s rotary axis ), DMG chose for instance a DRP, a TwinDrive combination of two servo‐planetary reducers mounted together in a universal housing and offering a true turnkey drive solution.
Pure mechatronics – under one roof
A quick glance into the design of the DMU 600P easily shows REDEX’ ability to offer many other high‐class drives for machine tool manufacturer alongside the „Twin Drive“ rack & pinion solution.
Compact, high performance RAM series two‐speed gearbox (Fig. 4) is for instance also used inside the machine main spindle, when the milling head changer is driven by a “SingleDrive”, using SRP servo‐planetary reducer.
Thus, DMG did use there the principle of „everything under one roof“, by choosing the same supplier for all the drive axis on this high performances machine. And it wouldn’t have been possible without the wide product range in REDEX’ portfolio which gives a technical answer to almost any of the engineer’s requirements.
In addition, at last, another key issue for DMG was the extensive support given by REDEX from the early design phase to the final commissioning. This is of huge importance, especially when a rack & pinion drive is being used for the first time. Through several calculations, optimisation and
design advices, as well as through setting up assistance at the workshop, REDEX were able to offer high added value assistance in the use of machine‐tool drives, thus making a significant contribution towards the success of the machine.
A worldwide success! As Florian Garbarsky finally added: „The DMU P‐series machines are marketed across the globe and are in heavy demand for precise, quick and cost‐effective machining of large components.“
Picture captions
Figure 1 (DMU 600 P ‐ complete)
Figure 2 (DMU 600 P – structure showing the main axis)
The DMU 600P 5‐axis portal milling machine was developed for precise and flexible machining of large components.
Figure 3 (DMU 600 P – X‐axis)
DRP TwinDrive shown at the other end of the X‐axis rack
Figure 4 ( DRP TwinDrive)
The zero‐backlash Twin Drive turnkey concept enables high positional accuracy on the 6 meters travel of the X axis.
Figure 5 (RAM High‐torque)
The two‐speed gearbox integrated inline inside the RAM gives ability to work at low speed‐high torque for rough machining and high speed‐low torque for high quality finishing.
Pictures: 1‐2‐3 DMG, 3‐4 REDEX
The tool part weighs several tons and are usually several meters long but every micrometer is crucial.
Precise machining of heavy components
DMG have developed the DMU P‐series portal milling machines for this exact purpose. The largest model in the series DMU 600P (Fig 1) is especially designed for precise, quick machining in XXL dimensions and performs milling and turning operations with high precision at maximum travels of 6000 x 4200 x 1500 mm (X/Y/Z‐Axis) and up to 2000 mm in the W‐axis. The rough parts weight may be up to 40 tons. At the same time the DMU 600P guarantees top speed and maximum flexibility since this machine has been designed for 5‐axis turning and milling in a single setup.
High precision with long travel lengths
One of the biggest challenges for the DMG designers was to guarantee such high level of machining precision at such large travel lengths (Fig. 2).
Linear drives play a central role here. Florian Garbarsky, Project Manager at DMG in Pfronten:
„The drives must have zero‐backlash with repeatable precision over thousands of operating hours and facing high forces directly related to the 60 kW power of the motor spindle.“
In figures: over a travel of 6 metres, an accuracy of up to +/‐ 0,0075mm is reached, with accelerations up to 3 m/s2. Thus, the highest level of accuracy, stiffness and the most constant temperature are considered as prerequisites when designing the complete machine. With these travel lengths and accuracy levels requests in hand, ball screws technology wasn’t considered to become a real challenger.
Rack & pinion drives
To guarantee the stiffness level, DMG designers have taken great care in selecting suitable drive systems. As said Florian Garbarsky: ‘’We carried out extensive benchmarking before to decide to use zero‐backlash rack & pinion drives from REDEX’’. Even in the C‐axis (the rotary axis of the spindle head), a ‘TwinDrive’ precision drive ensures high precision motion and positioning. It’s also noticeable that the two vertical ball screws of the W‐portal axis are synchronized through two SRP2 servo‐planetary reducers from REDEX.
Spindle Drive
In order to offer the high productivity high‐torque‐at‐low‐speed feature, a water cooled twospeed gearbox from the REDEX’ RAM series has been also mounted „inline“ (between the drive motor and the spindle inside the RAM).
X‐ and Y‐Axis: zero‐backlash „Twin Drive“‐ rack & pinion drive
According to its mechanical principle, there is always a certain backlash which affects the position accuracy on conventional rack & pinion drives. But this limitation does not apply to the TwinDrive‐Systems from REDEX, as the company has found a way to offer 100% zero‐backlash rack & pinion drives. The basic principle: two electronically synchronised complete drives are used in parallel, (motor + planetary reducer). One of the two servo motors serves as a drive, the other acts as a brake and thus ensures constant preload between the two pinions and the rack. This solution fully cancels the backlash and offers the most precise motion and positioning. And it’s this principle which was applied to the 6000 mm long X‐axis of the DMU 600P, as well as to the 4200 mm long Y‐axis and the C‐circular axis.
In the X‐axis, the turnkey drive solution DRP was chosen, including its two planetary drives with their two servo motors (Fig. 3).
In the Y‐axis the choice was rather to use the KRPX planetary reducers, which are fitted left and right on the Z‐carriage of the machine. And then, a DRP was used again on the spindle rotary axis (C‐axis). The machine’s CN electronic control then takes over the synchronisation and the preload for each of these TwinDrive systems.
High acceleration and maximum precision thanks to rigid linear drives
If the zero‐backlash feature of the drives is absolutely mandatory, it’s not enough by itself for reaching the requested level of maximum precision and best surfaces quality.
Just as important are the global stiffness, the control of temperature variations and an excellent transmission error accuracy – exactly the features which are the core strengths of REDEX planetary gearboxes. Thus the drives are extremely rigid in all directions, leading to outstanding positional accuracy, machined surface and repeatability.
To guarantee these features, the gearboxes are fitted with solid output bearings and the pinion is directly integrated into the pinion shaft. The bearing assembly itself consists of two pre‐loaded, oversized tapered roller bearings, which are fitted at the closest to the contact point of the pinions. The gearbox housing itself is machined extremely precisely and its design was widely optimized for offering maximum rigidity, whatever are the load directions.
This design not only guarantees very high torque rigidity, but also the best stiffness figures in all other directions, including the radial bending, which is ‐according to the extensive tests conducted by REDEX‐ responsible for almost 60 % of the total distortion in a rack & pinion drive application.
Thus, the bending is sharply reduced, and the axis natural frequency is highly improved allowing higher acceleration rates, heavier moved masses, while meeting higher precision requirements.
Benefits are not only technical, but also economical
Last but not least, for DMG, REDEX’s drive concept wins the argument not only from a technical viewpoint but also from an economic perspective.
According to an extended cost study by the OEM, optimum TCO* offered by REDEX for a travel of
6 m on the X‐axis with its rack & pinion drives cannot be beaten by any other technical solution of similar accuracy.
A multi‐facetted concept
The extended REDEX’ products range dedicated to Machine‐tool Drives applications allows engineers to make their choice in an almost unlimited library of drives, whatever are their level of technical requirements.
REDEX offer its Rack & Pinion concept in different variants – for instance with mechanical or electrical pre‐load, whereby DMG opted for electrical synchronization. On the other hand the systems may include any of the usual types of servo motor and gearbox/ gearbox assemblies.
For the DMU 600P C‐axis, (the spindle’s rotary axis ), DMG chose for instance a DRP, a TwinDrive combination of two servo‐planetary reducers mounted together in a universal housing and offering a true turnkey drive solution.
Pure mechatronics – under one roof
A quick glance into the design of the DMU 600P easily shows REDEX’ ability to offer many other high‐class drives for machine tool manufacturer alongside the „Twin Drive“ rack & pinion solution.
Compact, high performance RAM series two‐speed gearbox (Fig. 4) is for instance also used inside the machine main spindle, when the milling head changer is driven by a “SingleDrive”, using SRP servo‐planetary reducer.
Thus, DMG did use there the principle of „everything under one roof“, by choosing the same supplier for all the drive axis on this high performances machine. And it wouldn’t have been possible without the wide product range in REDEX’ portfolio which gives a technical answer to almost any of the engineer’s requirements.
In addition, at last, another key issue for DMG was the extensive support given by REDEX from the early design phase to the final commissioning. This is of huge importance, especially when a rack & pinion drive is being used for the first time. Through several calculations, optimisation and
design advices, as well as through setting up assistance at the workshop, REDEX were able to offer high added value assistance in the use of machine‐tool drives, thus making a significant contribution towards the success of the machine.
A worldwide success! As Florian Garbarsky finally added: „The DMU P‐series machines are marketed across the globe and are in heavy demand for precise, quick and cost‐effective machining of large components.“
Picture captions
Figure 1 (DMU 600 P ‐ complete)
Figure 2 (DMU 600 P – structure showing the main axis)
The DMU 600P 5‐axis portal milling machine was developed for precise and flexible machining of large components.
Figure 3 (DMU 600 P – X‐axis)
DRP TwinDrive shown at the other end of the X‐axis rack
Figure 4 ( DRP TwinDrive)
The zero‐backlash Twin Drive turnkey concept enables high positional accuracy on the 6 meters travel of the X axis.
Figure 5 (RAM High‐torque)
The two‐speed gearbox integrated inline inside the RAM gives ability to work at low speed‐high torque for rough machining and high speed‐low torque for high quality finishing.
Pictures: 1‐2‐3 DMG, 3‐4 REDEX