www.indo-industry.com
03
'18
Written on Modified on
Fakta tentang Efisiensi Produksi Manufaktur Dewasa Ini
Perusahaan manufaktur umumnya berupaya untuk memproduksi sejumlah komponen dengan kualitas tertentu, dalam waktu tertentu, serta dengan biaya tertentu. Mereka berupaya untuk mencapai target ini secara konsisten dengan mengendalikan berbagai faktor, termasuk parameter pemotongan, biaya tool, waktu penggantian, pemanfaatan machine tool, biaya penanganan benda kerja, serta biaya material dan tenaga kerja.
Efisiensi produksi adalah seni dan ilmu tentang menyeimbangkan faktor proses untuk mencapai hasil yang diinginkan. Selama lebih dari dua abad dalam sejarah pengerjaan dengan mesin, elemen efisiensi produksi meningkat beberapa kali lipat. Proses manufaktur di tahap awal berkembang dari produksi yang menghasilkan satu item tunggal yang dibuat oleh pengrajin hingga kemudian sampai pada produksi komponen secara massal yang telah terstandardisasi dengan menggunakan machining tool. Perkembangan metode manufaktur telah memunculkan produksi massal generasi kedua yang menghasilkan lini produksi dan output yang meningkat signifikan dalam hal jumlah komponen yang identik: skenario volume tinggi, varian produk yang rendah (HVLM). Kemudian dilanjutkan dengan robot dan mesin CNC yang mengembangkan efisiensi produksi massal generasi ketiga. Dan yang terbaru adalah penggunaan teknologi digital yang diterapkan dalam pemrograman, kontrol machine tool, dan sistem penanganan benda kerja yang memunculkan produksi manufaktur generasi keempat, dikenal dengan Industry 4.0, yang memungkinkan penghematan biaya produksi untuk menghasilkan varian tinggi dan volume rendah (HMLV).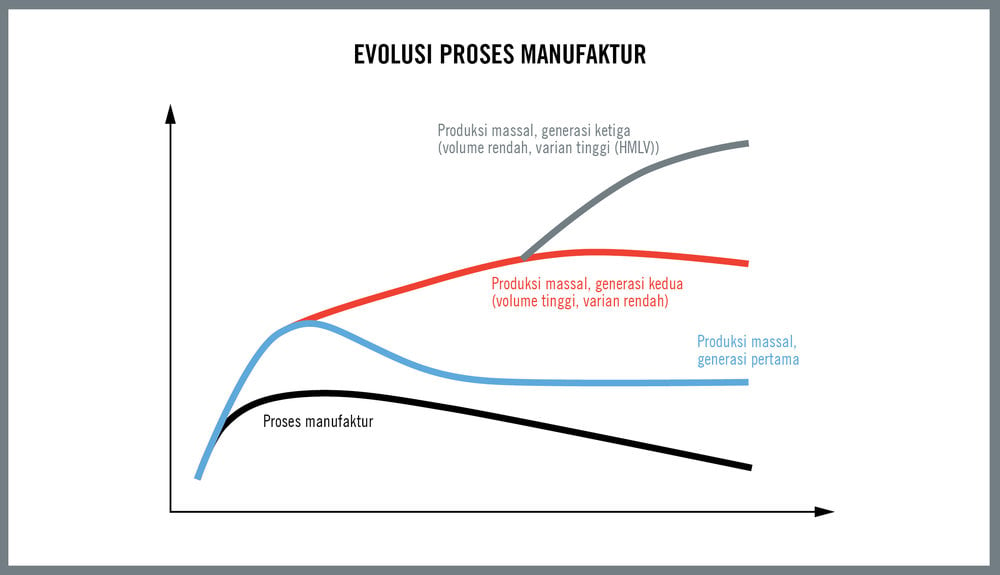
HQ_POS_Manufacturing_Process_Evolution.jpg
Untuk beralih secara efektif dari metode produksi HVLM ke HMLV, manufaktur perlu mengenali fakta perubahan dan perkembangan tentang efisiensi produksi serta memanfaatkan informasi dan teknologi yang tersedia untuk menganalisis operasi dan memenuhi target mereka. Elemen penting dari transformasi ini termasuk mengesampingkan keyakinan dan praktik yang terlalu menyepelekan serta mengungkap biaya terselubung yang dapat menghambat upaya dalam memaksimalkan produktivitas.
Volume Tinggi, Varian Rendah, Efisiensi Sederhana?
Proses pengerjaan dengan mesin yang terstandardisasi dikembangkan pada abad ke-19 guna mempercepat dalam menghasilkan produk yang identik dengan komponen yang dapat saling dipertukarkan. Manufaktur otomotif menyempurnakan pendekatan HVLM ini ke tingkat yang maksimum, dengan menetapkan lini transfer dan metode lain untuk memproduksi ratusan ribu atau jutaan komponen yang sama selama bertahun-tahun.
Karakteristik jangka panjang pada metode produksi HVLM memungkinkan manufaktur untuk menyempurnakan berbagai faktor proses untuk memperoleh output maksimum, konsistensi, dan biaya yang rendah. Teknologi pendukung termasuk pengganti tool dan palet serta robot semakin meminimalkan variasi yang dihasilkan. Hal ini dapat dicapai dengan asumsi bahwa operasi berjalan dengan sempurna dan memberikan hasil 100 persen dengan biaya yang dapat diprediksi, tidak ada waktu henti yang tidak direncanakan, tidak ada hasil yang cacat, tidak ada pengerjaan ulang, dan tidak ada operasi sekunder seperti melakukan penghalusan permukaan.
Salah satu asumsi yang digunakan biasanya adalah biaya tool sekitar tiga persen dari total biaya produksi. Angka tiga persen adalah tolak ukur yang cukup dapat diterima tetapi jarang sekali valid. Karakteristik pengerjaan material benda kerja, misalnya, ternyata memiliki efek yang besar; pergantian material dari baja ke titanium dalam memproduksi suatu komponen dapat meningkatkan penggunaan tool sebesar lima kali lipat. Proporsi tiga persen tersebut bisa menjadi 15 persen, semua faktor lainnya kurang lebih sama.
Berfokus pada waktu penggunaan tool semata dapat menyebabkan faktor lain, seperti waktu henti untuk pergantian tool, menjadi terabaikan. Pendekatan ini tidak sesuai dengan fakta yang ada. Manufaktur harus memahami bahwa waktu pengerjaan, waktu penyiapan, waktu penggantian tool, memasukkan dan mengeluarkan, serta faktor lain saling memengaruhi satu sama lain.
Contoh sederhana dari interaksi faktor proses yang tidak diantisipasi ini adalah produksi yang memerlukan waktu pemotongan selama dua menit dan total waktu sekitar dua menit untuk memasukkan dan mengeluarkan benda kerja. Penggantian tool memerlukan waktu satu menit, dan masa pakai tool dapat digunakan untuk menghasilkan lima benda kerja, sehingga waktu untuk penggantian tool sekitar 0,20 menit per komponen. Karena setiap komponen memerlukan waktu pemrosesan selama 4,2 menit, outputnya adalah sekitar 14 benda kerja per jam. Setiap tool berharga 15 euro, dengan masa pakai tool yang hanya menghasilkan lima benda kerja, berarti diperlukan 2,8 tool (42 euro) untuk menghasilkan 14 benda kerja. Biaya pengerjaan adalah sebesar 50 euro per jam. Jadi total biaya produksi untuk menghasilkan 14 benda kerja tersebut adalah 92 euro.
Kemudian, dalam upaya untuk mempercepat output dan produktivitas, perusahaan manufaktur mempercepat waktu pemotongan sebesar 10 persen. Hal ini mengurangi waktu pemotongan sebesar 10 persen (menjadi 1,8 menit) tetapi juga memangkas masa pakai tool hingga menjadi setengahnya, artinya satu cutting edge hanya akan menghasilkan dua setengah benda kerja sebelum kemudian perlu diganti. Waktu penggantian tool masih tetap satu menit dan memasukkan/mengeluarkan benda kerja selama dua menit. Waktu produksi untuk satu benda kerja masih tetap 4,2 menit (1,8 menit untuk pemotongan, 2 menit untuk manipulasi benda kerja, dan 0,4 menit untuk penggantian tool) atau 14 benda kerja per jam. Biaya pengerjaan dan tool masih tetap sama, tetapi kini diperlukan 5,6 tool (biaya tool 84 euro) per jam produksi. Meskipun upaya tersebut adalah untuk meningkatkan kecepatan output, waktu produksi untuk menghasilkan 14 benda kerja masih tetap sama, namun biayanya meningkat dari 92 euro menjadi 134 euro.
Dalam kasus ini, meningkatkan kecepatan pemotongan tidak serta merta membuat pengoperasian lebih produktif. Mengubah waktu pemotongan dapat berpengaruh pada faktor lain dalam sistem pengerjaan mesin, seperti dalam contoh ini, masa pakai tool dan waktu penggantian tool. Oleh karena itu, perusahaan manufaktur harus mempertimbangkan konsekuensi perubahan proses ini dengan cermat.
Bentuk lain dari biaya tersembunyi adalah mengenai pelaksanaan langkah dalam proses. Di banyak perusahaan manufaktur, misalnya, waktu yang dihabiskan untuk mengganti insert, adalah kasus yang umum tentang biaya tersembunyi. Waktu yang ditetapkan untuk mengganti insert mungkin hanya satu menit. Akan tetapi, ketika diukur pada kenyataannya di ruang produksi, waktu penggantian tersebut bisa menjadi dua, tiga, atau sepuluh menit, perbedaannya sebesar 60 hingga 600 detik.
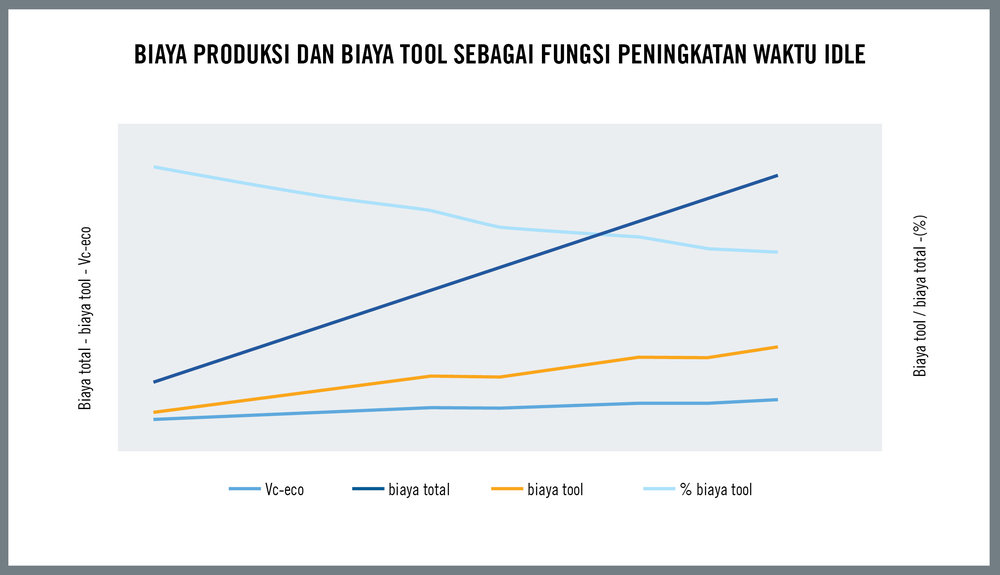
HQ_ILL_Production_Cost_And_Tooling_As_A_Function_Of_Increasing_Idle_Times.jpg
Gambar 2
Varian Tinggi, Volume Rendah, Pertimbangan Kompleks
Dewasa ini, persaingan global memaksa manufaktur untuk memproduksi varian berbeda pada produk mereka agar dapat memenuhi kebutuhan dari sebagian kecil pengguna mereka. Teknologi komputasi yang canggih memungkinkan perubahan pesat pada desain komponen dan program pengerjaannya, serta memudahkan dalam melacak variasi produk dan inventaris. Hal ini menghasilkan pergeseran ke skenario produksi varian lebih tinggi dengan volume lebih rendah (HMLV). Kini, pendekatan ini telah dikembangkan secara memadai yang memungkinkan untuk memproduksi dengan efisien untuk beberapa item atau bahkan satu item komponen.
Rentang waktu yang lebih panjang pada skenario produksi HVLM memungkinkan untuk perencanaan yang tidak tergesa-gesa dan penyempurnaan faktor proses. Perencanaan dilakukan secara berbeda untuk situasi HMLV. Teknologi rekayasa teknik dan inventaris yang terkomputerisasi mendukung perubahan yang cepat dalam hal jenis produk dan output, akan tetapi konsekuensinya, proses perencanaan HMLV tersebut kompleks dan reaktif. Pesanan untuk sepuluh komponen dapat diikuti oleh pesanan sejumlah lot yang terdiri dari dua atau lima komponen yang berbeda, atau bahkan satu item. Material benda kerja dapat berubah dari baja ke aluminium atau titanium, dan geometri komponen berubah dari sederhana menjadi kompleks. Sementara, tidak cukup waktu yang tersedia untuk menentukan masa pakai tool melalui uji coba.
Untuk mengelola masa pakai tool pada situasi HMLV, perusahaan manufaktur biasanya menggunakan perkiraan konservatif mengenai proyeksi masa pakai tool dan, untuk amannya, menggunakan tool baru untuk setiap pengoperasian, dengan membuang tool sebelum mencapai masa pakai produktif penuhnya. Waktu pemotongan hanyalah satu faktor dalam gambaran besar proses produksi. Dalam produksi HMLV, waktu yang diperlukan untuk memanipulasi benda kerja dan bagian peralatan yang berbeda, mengganti tool, dan mengganti insert sering kali lebih lama dibandingkan waktu pemotongan yang sebenarnya. Faktor tool, machine tool, waktu henti, tenaga kerja langsung, material benda kerja dapat mencakup biaya terselubung. Pendekatan terbaru untuk efisiensi produksi memperhitungkan biaya tool dan biaya material benda kerja, biaya peralatan dan produksi, biaya peralatan selama waktu henti, serta gaji dan biaya perawatan.
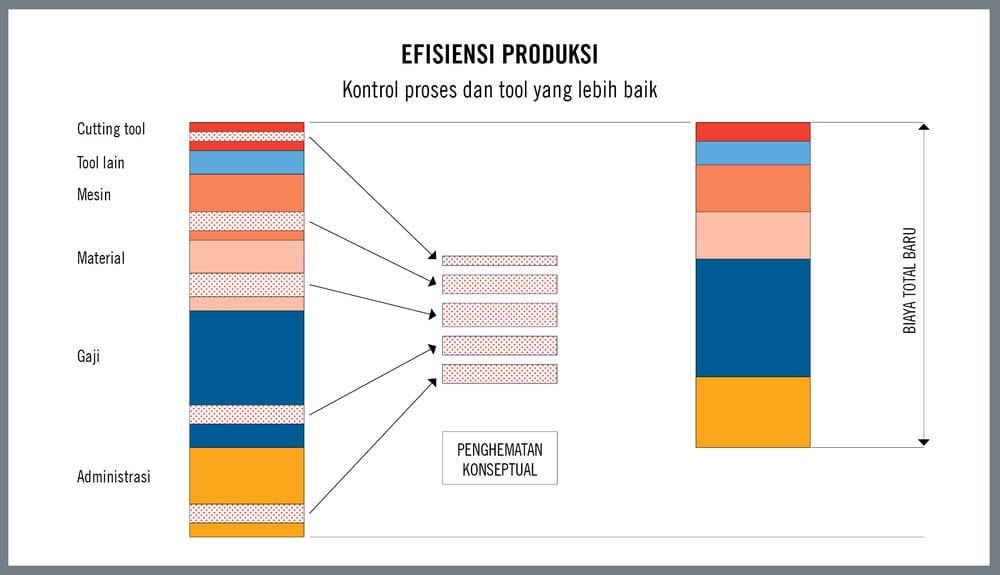
HQ_ILL_Production_Economics
Gambar 3
Perubahan kriteria produksi HMLV yang cepat meningkatkan kesulitan untuk mencapai hasil produk dengan persentase yang tinggi. Dalam kasus produksi HVLM yang beroperasi dalam waktu yang panjang, uji coba dan penyesuaian dapat menghasilkan persentase hasil sebesar sembilan puluh persen. Di sisi lain, hasil produksi HMLV bisa bersifat biner. Pengoperasian satu komponen yang berhasil dapat memberikan hasil produksi sebesar 100 persen, tetapi bila komponen tersebut tidak dapat diterima atau benda kerja tersebut gagal, maka hasilnya adalah nol. Tuntutan akan kualitas dan biaya serta efisiensi waktunya tetap sama, tetapi hasil yang pertama menjadi persyaratan utama. Dalam kasus seperti ini, menghindari rusaknya tool mungkin menjadi pertimbangan yang paling penting. Satu keuntungan yang didapat adalah keausan tool menjadi kekhawatiran minimal dalam situasi pengoperasian singkat dan perusahaan manufaktur dapat menerapkan, dalam batas kewajaran, parameter pemotongan yang lebih agresif dan produktif.
Variabel yang terkait adalah menentukan kapan saat yang tepat untuk mengganti tool. Menunggu terlalu lama bisa mengakibatkan tool rusak, atau sekurangnya dapat mengganggu produksi, atau menghasilkan benda kerja yang rusak. Sebaliknya, mengganti tool yang terlalu sering akan meningkatkan biaya dalam hal biaya tool itu sendiri serta waktu yang hilang ketika mesin dihentikan dan tool diganti. Menentukan kapan waktunya mengganti tool memerlukan evaluasi hubungan antara perubahan tersebut dalam seluruh sistem pengerjaan dengan mesin, membuat protokol penggantian tool, dan kemudian mematuhi protokol tersebut secara disiplin.
Kesimpulan
Hubungan antar-faktor di dalam sistem pemotongan logam tidaklah satu berbanding satu. Mengubah kondisi pemotongan, material benda kerja, atau volume produk akan memengaruhi masa pakai tool serta berbagai aspek lain dalam sistem pengerjaan dengan mesin. Tantangan efisiensi produksi pada fasilitas manufaktur adalah menyadari hubungan antara-faktor ini dan mengembangkan strategi untuk mengatasinya dengan cara yang pragmatis. Sayangnya, setiap operator manufaktur bukanlah profesor di bidang matematika dan mereka tidak memiliki banyak waktu untuk menggali lebih dalam mengenai hubungan antar-faktor tersebut. Oleh karena itu, pemasok menawarkan layanan analisis dan manajemen proses (Lihat artikel singkat) yang memberi gambaran komprehensif kepada manufaktur tentang operasi spesifik mereka, serta memberi arahan mengenai cara untuk memaksimalkan kekuatan produktivitas dan efisiensi dalam upaya mereka.
Yang sering menjadi keluhan pemilik manufaktur adalah bahwa mereka memiliki cukup banyak pekerjaan dan pelanggan yang membayar, tetapi masih tetap saja kehilangan uang. Solusi terhadap masalah mereka adalah dengan mengenali fakta tentang banyaknya faktor yang terlibat dalam efisiensi produksi saat ini, serta menyingkap dan menghilangkan biaya yang
tersembunyi, sehingga operasi manufaktur mereka dapat memperoleh hasil maksimum.
Artikel singkat
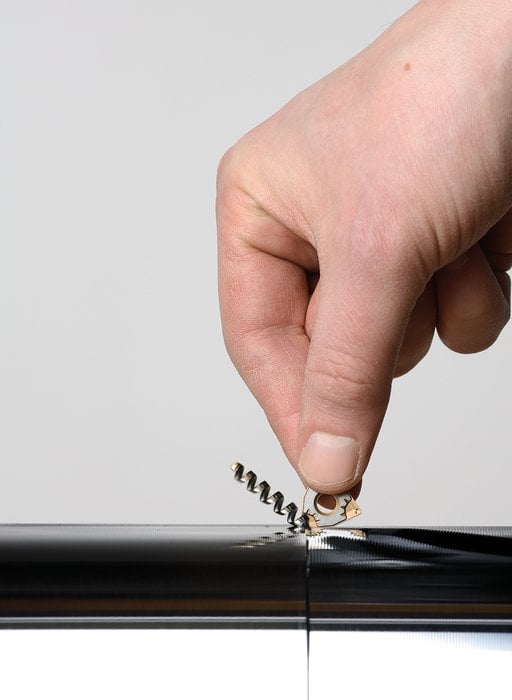
HQ_IMG_Duratomic_Chip.jpg
Gambar 4
Analisis Otomatis
Dari sejak diperkenalkannya produksi massal, sejumlah faktor yang memengaruhi produktivitas dan biaya manufaktur telah meningkat berkali lipat. Seiring semakin kompleksnya operasi pengerjaan dan perkembangan peralatan, demikian pula hubungan antar-elemen di dalam sistem manufaktur. Tidak satu pun elemen ini yang berdiri sendiri. Mengubah kriteria volume output, misalnya, akan memengaruhi biaya tool, peralatan, perawatan, tenaga kerja, dan biaya lainnya.
Menentukan sejumlah faktor yang terlibat dan hubungan antar-faktor tersebut satu sama lain merupakan tantangan besar yang tersendiri. Kompleksitas ini memerlukan pendekatan yang sistematis untuk mengukur, mengontrol, dan mengelola proses manufaktur.
Sistem Analisis Biaya Produktivitas (Productivity Cost Analysis, PCA) dari Seco menguji keseluruhan proses manufaktur guna menemukan cara untuk mengurangi biaya dan meningkatkan produktivitas. Basis dari sistem ini adalah pengalaman dan pengetahuan manufaktur Seco secara global selama beberapa dekade ini. Seco menerapkan pengetahuan tersebut dipadu dengan analisis dan algoritme komputer yang canggih, termasuk teknik simulasi Monte Carlo yang memungkinkan otomatisasi modeling biaya.
Perwakilan Seco yang berkualifikasi melakukan PCA dengan mengevaluasi semua tool dan teknologi yang digunakan dalam proses untuk menghasilkan laporan yang komprehensif yang meliputi informasi proses, seperti data penggunaan tool dan pemotongan, dan informasi biaya yang meliputi biaya per komponen, output per jam, dan biaya investasi. PCA dapat mengevaluasi pemrosesan benda kerja mulai dari operasi satu tool hingga operasi proses produksi yang lengkap di pabrik manufaktur.
Fokusnya adalah peningkatan produktivitas yang memiliki dampak terbesar terhadap biaya. Sistem ini mempertimbangkan berbagai kendala atau batasan operasional dan dapat mengenali bagian mana yang memerlukan penelitian yang mendalam.
Pada tahap awal penerapan perangkat lunak PCA, dimulai dengan meneliti tolak ukur waktu dan biaya pada operasi subjek atau fasilitas, dengan meninjau faktor tool yang meliputi parameter proses, waktu siklus, dan kriteria hasil. Pada tahap kedua, adalah melibatkan proses yang sama, tetapi dengan melakukan penyesuaian dalam kondisi pemotongan dan tool yang digunakan. Pada tahap ketiga dapat melibatkan perubahan dalam proses, dengan mengombinasikan operasi dan eksplorasi perubahan yang lebih besar, seperti upgrade machine tool.
Manufaktur yang menggunakan sistem PCA dari Seco secara umum dapat memperkirakan keuntungan dari penghematan biaya total hingga sebesar 30 persen dan peningkatan produktivitas sebesar 40 persen, terlepas dari sektor industri yang mereka layani.
Oleh:
Patrick de Vos, Corporate Technical Education Manager, Seco Tools