www.indo-industry.com
19
'22
Written on Modified on
Cartonnages Vaillant tools up with new EXPERTCUT die-cutter from BOBST
The French manufacturer is one of the first in the world to take delivery of the new EXPERTCUT 2.1 Autoplaten® die-cutter with TooLink technology, installed recently to increase productivity and expand opportunities in corrugated board packaging with the widest variety of e-commerce and FMCG (fast moving consumer goods) boxes.
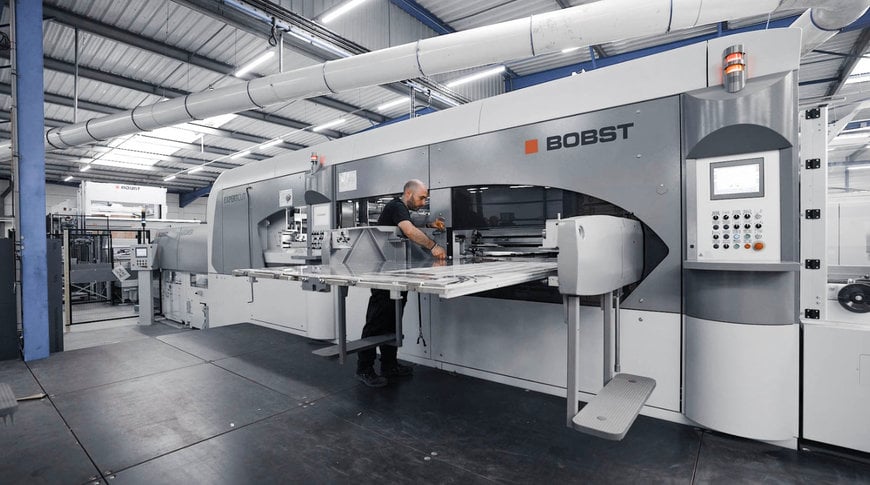
Situated in Lambres-lez-Aire, Pas-de-Calais, Cartonnages Vaillant was founded in 1957 by Fernand Vaillant. Since 2014, the French packaging producer has been part of Bulteau Développement Group giving it the security and support of a large corporation, while retaining the flexibility and responsiveness of an independent business.
“We often refer to ourselves as packaging generalists when talking about our business, because we manufacture all types of packaging and strive to add value wherever possible,” “To maintain our top position in the region, we continue to invest in industry-leading machinery that allows us to support our customers with high quality corrugated products and fast delivery times,” said Director Bruno Delannoy.
The new BOBST EXPERTCUT 2.1 has joined the more than 40 diverse pieces of equipment that are in operation at Vaillant’s modern production facility, including several from BOBST. The state-of-the-art Autoplaten® die-cutter has been brought in to expand the company’s capabilities to the larger 2.1 metre format and to match the productivity of the existing printing machines.
“BOBST and Vaillant have a long history and we have built a great partnership between us. We have bought a number of folder-gluers and die-cutting machines from the Swiss manufacturer over the years, so we have a lot of real-life experience with their excellent products,” Deputy Director Christophe Normand added.
Exceptional precision and impressive productivity
Introduced to the market in 2022, the EXPERTCUT 2.1 – along with the smaller 1.7 model – completes BOBST’s portfolio of mid-range die-cutters for the corrugated board industry. These industry-leading machines come fitted with a wealth of new design and automation features, which have been developed to guarantee maximum uptime, perfect sheet feeding and precise die-cutting.
The platen section has been completely redesigned to reduce makeready and set-up times, as well as the cutting force needed to produce perfect blanks, resulting in substantially increased productivity and longer tool life. The sheet transport has also been optimized with double-cam gripper bar advance, which makes acceleration and deceleration of the sheets incredibly consistent and smooth.
With changeovers taking less than eight minutes, the EXPERTCUT gives Vaillant the flexibility to address both long and short production runs of corrugated board in a maximum size of 2,100 x 1,300 mm (82.67 x 51.18 in) and 0.75–9 mm (0.03–0.35 in) in thickness. The speed of production also makes this machine extremely competitive. Up to 5,500 sheets can be converted each hour, equivalent to an impressive 20 million square meters per year.
Operator safety is a priority for Vaillant as Mr Delannoy explained: “BOBST has adapted the EXPERTCUT precisely in terms of safety to protect the personnel working on this machine while producing at optimal rates to keep us competitive.” He added, “If we want to attract new talent and improve the skills of our employees, we must continue to invest in this type of innovative equipment.”
Commenting on the redesign of the BOBST machine, Mr Normand said, “It is also clear that a lot of effort has gone into the new design of the die-cutter; the aesthetics and ergonomics are much nicer than similar machines from the early 2000s, something our operators noticed immediately and enjoy every day.”
Full automation for non-stop operation
To fully leverage the power of BOBST innovation in corrugated production, the EXPERTCUT 2.1 die-cutter at Vaillant has been set up with LOADER AF to ensure a consistent stream of boards is fed to the machine, and a BREAKER 2 FLAT TRACK blank separator which works in combination with the PALLETIZER module, offering the company a fully automated production line without the need for operator intervention.
For this beta machine, Vaillant also chose to include TooLink technology. Taking the human variables out of the equation, this digital solution connects tools, machinery and processes into one seamless workflow. Each cutting tool is fitted with a secured data chip which is used to identify it and to transfer all the setup parameters to the die-cutter automatically, saving significant amounts of time on repeat jobs.
“We have been considering Industry 4.0 for some time, and we just couldn’t resist the digital solution offered by the EXPERTCUT with TooLink,” “As well as saving time in the search for tools in the storage area, TooLink makes setup and adjustments on the machine much easier, because the automated job recipe management remembers the previous order settings. Additionally, it helps us measure the production times, uptimes, and the number of sheets produced, which means that we will be able to manage our daily operations much better at the ERP level,” said Mr Normand.
Successful integration for future success
Just a few months into production and the EXPERTCUT has made a great impression on the management team at Vaillant, who is clear about its potential.
“The new BOBST EXPERTCUT, which has already been successfully integrated into our production, will allow us to remain the number one in packaging and e-commerce in Hauts de France. With its exceptional productivity, I believe that the machine will help us tremendously in achieving our goals,” concluded Mr Delannoy.
www.bobst.com